Checkout our nationally #1 Google ranked blog post about how to build a workplace safety program.
Learn how to achieve compliance, protect your employees and business from harm, and get the piece of mind you deserve.
CLICK BELOW TO GET THE FREE WHITE PAPER NOW
SEE THE ORIGINAL BLOG POST BELOW
So you’re wondering how to start a workplace safety program at your company and not sure where to begin? Building an effective health and safety program for the first time is a major undertaking, so it’s important to gain some perspective and understanding of the basic requirements and challenges you’re likely to face along the way, so we’ve created this blog post in hopes of helping you do just that! Think of this article as an “Introduction to OSHA Compliance 101.”
With that said, let’s get on with it…
High Hazard Industries:
Let’s begin by making sure that your company needs a workplace safety program, because not every company does. To make a long story short, any company who’s operations exposes their employees to workplace health or safety hazards must take steps to mitigate those hazards by developing and managing a workplace safety program. Here’s a brief list of common industries that just about always have workplace health and safety hazards: manufacturing, construction, industrial services, warehousing/distribution, healthcare and even certain retail businesses.
If your company is in one of these industries, then there’s a very high probability that you’ll need to develop and manage an OSHA compliance program and the rest of this blog post describes the fundamentals of what that means.
Workplace Health & Safety Hazards:
So what exactly are workplace health and safety hazards? Unfortunately, there’s a wide range of health and safety hazards that if not properly managed, can result in serious employee injuries, illnesses and in extreme cases can even lead to death.
Safety Hazards:
Some of the more common safety hazards include falls from heights, struck-by and caught-between, accidental release of hazardous energy (electrical and mechanical), unguarded machinery, chemical burns, fires, and even workplace violence.
Health Hazards:
In addition to these safety hazards, there’s also a long list of health hazards that must be managed too. These include exposures to toxic chemicals & metals and/or other contaminants such as dust or bodily fluids that can lead to serious health problems. Then there’s potential exposure to excessive noise levels which can result in hearing loss over time.
So there you have it, we’re off to a good start: if your company is in a high hazard industry which exposes your employees to potentially harmful health and safety hazards, then you’ll need to develop a workplace heath and safety program to help protect your employees from those hazards.
Sounds great, but what exactly does that mean and how do you do that?
Controlling Hazards:
Ok, so let’s try to simplify things a little. Think of a workplace safety program as nothing more than a set of “controls” which are put into place to help protect employees from the potential harm posed by workplace health and safety hazards.
Actually, there’s a recommended hierarchy of health and safety controls as follows:
- Elimination: The best option is to eliminate the hazard if at all possible. for example, a company could scrap an old and damaged forklift that is no longer safe to operate.
- Substitution: Substitute the hazard with something less hazardous. For example, a company could replace a hazardous chemical with a non-hazardous chemical.
- Engineering controls: Machine guards to protect from pinch points, rotating parts, etc.
- Administrative controls: Use of safety policies and procedures, employee safety training, rotating employees to reduce excessive exposure to loud noises etc.
- Personal protective equipment: Safety glasses, hard hats, steel toed boots.
Notice that PPE (Personal Protective Equipment) is at the bottom of the list. PPE should be considered the last line of defense only after all other control options have been considered.
There’s much more to learn about this subject, but this should give you a good idea of what health and safety controls consist of. Again, each of these controls are intended to help mitigate the risks associated with workplace health and safety hazards.
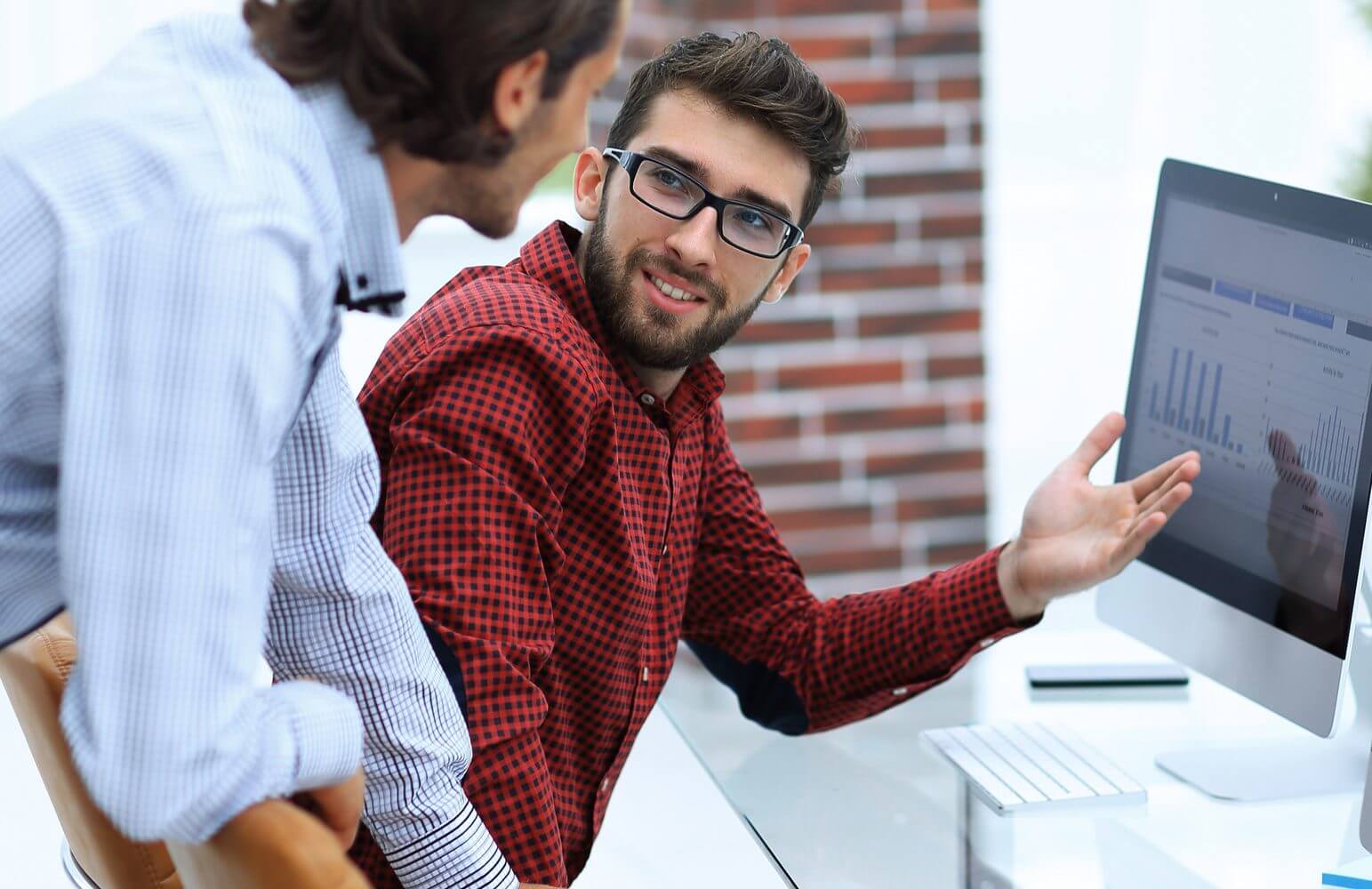
OSHA Standards:
In order to help employers manage health and safety issues, the Occupational Safety & Health Administration, or OSHA, has developed a series of Standards, each of which is designed to address most of the major hazards that exist in the workplace. For example, there’s a standard for fall hazards (Fall Protection), chemical hazards (Hazard Communication), noise hazards (Hearing Conservation), respiratory hazards (Respiratory Protection), forklifts (Powered Industrial Trucks), Control of Hazardous Energy (Lockout Tagout) and even standards to address toxic metals like lead. Each of these standards contain and specify various controls which are intended to help mitigate specific health or safety hazards.
Think of OSHA compliance as a “prevention program” which mandates that impacted employers manage these standards, and their associated controls, to help prevent workplace injuries and illnesses.
Let me give an example of an actual OSHA standard to help illustrate the point. The OSHA standard which addresses chemical safety, is called Hazard Communication (don’t ask me where they got this name, because I have no idea!). The standard addresses all of the various hazards posed by chemicals, including burns, fires, health impacts, etc. The primary controls included in this standard are as follows:
- Safety Data Sheets, aka SDS’s (formerly known as MSDSs) which spell out all of the hazards associated which every chemical known to man.
- Labeling: Manufacturers and employers must properly label chemical containers in order to communicate the hazards associated with the chemical (fire, burns, toxicity, etc.).
- Employee Training: The primary purpose of training is to educate workers on how to read and understand SDSs, safely handle chemicals, properly label chemical containers and how to dawn and doff Personal Protective Equipment.
- Personal Protective Equipment (“PPE”) needed to protect workers from chemical hazards such burns, inhalation, etc. PPE includes things like gloves, safety glasses, respirators, etc.
The idea being that if an employer implements and manages all elements and controls included in the Hazard Communication standard, then their employees should then be protected from the various hazards presented by the chemicals they use. Of course no standard is perfect, nor are people, so there’s obviously no guarantee that all future chemical injuries will be prevented, but at least the basic hazards and risks have been addressed.
Keep in mind that OSHA hasn’t developed standards to address ALL workplace health and safety hazards, only the most common and risky ones. For all other hazards, OSHA has a “catch- all” called the General Duty Clause which basically states that employers must identify and control any other recognized hazards, in order to protect their employees from potential harm. A simple example might be tearing down an old, wind damaged shade awning that employees stand under for smoking breaks, because the employer realizes that it could collapse at any time.
More on OSHA Standards & Compliance:
It’s worth pointing out that OSHA standards are only designed to address “baseline” hazards and risks, and that many of their standards and laws were developed way back in the early 1970’s and haven’t been updated since. As a result, companies are always advised to go “over and above” OSHA standards by referencing and following guidance from other more up to date health and safety agencies such as National Safety Council, ANSI, etc. Having said that, it’s tough enough for most small businesses to achieve OSHA compliance, so it’s always best to start there, and then worry about going “over and above” later down the road.
It’s also worth pointing out that OSHA standards are Federal laws that all impacted employers must follow or face the consequences. Companies who fail to do so face major fines and penalties that can run into the $tens and even $hundreds of thousands of dollars, and potential criminal liabilities if employees get killed as a result of employer negligence.
Conduct a Safety Assessment to Determine Which OSHA Standards Apply to Your Company:
At this point, you might be wondering how to determine which OSHA standards apply to your operations? And this question leads us to revealing the first major step that any company needs to take in order to begin the process of implementing an OSHA health and safety compliance program. And that first step is to conduct a health and safety audit or assessment of your company to: 1) determine which workplace hazards are present in your operations, which will then 2) determine which OSHA Standards apply to your business.
Ideally, the end result of a solid health and safety compliance assessment will provide a “roadmap to compliance” which spells out exactly what a company needs to do in order to achieve and manage their OSHA compliance requirements.
Correcting Health & Safety Hazards:
A good, comprehensive OSHA compliance audit not only identifies all relevant hazards, but also itemizes all violations and recommended corrective actions for each. These corrective actions will include reference to relevant OSHA standards and the specific controls and elements that are required to abate the violation such as engineering controls, written procedures, training, testing, PPE, etc.. The audit would also address other “administrative” deficiencies and requirements such as record keeping (ie: OSHA 300 logs) and reporting requirements.
Typically, the first step after completing a health and safety audit is correcting any and all physical hazards identified in the workplace, since these often pose the greatest immediate risk to employees. These hazards include things like machine guarding issues, faulty extension cords, defective ladders, unlabeled chemical containers, lack of fall protection, etc.
Your Health & Safety Manual:
While correcting these physical hazards, it’s a good idea to begin working on the next major project which is developing your customized health and safety manual. This document, or group of individual written programs, will contain all of the specific OSHA standards which apply to the company as well as assigning key roles, etc. This document essentially becomes the company’s “safety bible” and spells out exactly what the company needs to do in order to implement and manage their workplace safety program.
To give you a better idea of what a safety manual might contain, let’s take a typical manufacturing company as an example. Such a manual might contain the following standards: Hazard Communication, Ladders, Personal Protective Equipment, Lockout/Tagout, Respiratory Protection, Emergency Action Plan, Fall Protection, Cranes and Hoists, Hearing Conservation, Powered Industrial Trucks and maybe more.
On a related note, many companies make the mistake of downloading a generic safety manual which will normally contain information and standards that don’t necessarily apply to that business. Again, the manual must be customized to your company’s specific operations and hazards!
More on Employee Safety Training:
This blog post wouldn’t be complete without taking a closer look at OSHA health and safety training requirements because this is one of the toughest requirements to comply with, especially for small businesses.
Again, just about all OSHA standards contain employee training requirements designed to help make employees aware of workplace health and safety hazards and how to avoid and manage them. Conducting effective and comprehensive training is essential to the success of any workplace safety program, yet it’s one of the toughest controls to manage and therefore one of the most commonly cited violations.
Why is health and safety training so tough to manage?
- Training must be customized to your operations: Many companies make the mistake of using generic videos or on-line resources. Technically this is a violation of OSHA standards, because training must be customized to address the specific hazards present in a company’s operations.
- Trainer must be competent: Companies who are serious about managing OSHA compliance will conduct live training sessions using competent trainers who understand the technical aspects of each standard, can engage their employees, and can answer employee questions. Many companies make the mistake of tasking managers and supervisors who lack the qualifications and experience to adequately train employees, which often ends up being a waste of time.
- Training is time consuming: most training topics take between 30-60 minutes to properly train, and some topics take much longer. Many companies make the mistake of believing that 10-15 minute “tailgate topics” are sufficient to meet OSHA standards, but they’re not.
- Frequency requirements: OSHA requirements that some topics only be trained once, but many have annual training requirements. Even though not all topics are required to be trained annually, OSHA recommends that all topics be trained annually.
- Employee turnover: Since most companies have employee turnover issues, and since OSHA requires that all impacted employees get trained, training becomes a never ending process for most companies.
Add it all up, and it’s clear that OSHA training is an expensive and inconvenient undertaking. And if all of these challenges aren’t tough enough to deal with, employers must also commit to pulling employees off the production line to get trained. This results in added payroll costs, production delays and other related disruptions.
Summary: Managing OSHA Compliance Is A Never Ending Process
Never forget that each of OSHA’s standards contain an extensive list of controls and elements that employers must implement and manage on an ongoing basis. These controls include ongoing employee training, conducting evacuation drills, developing equipment specific LOTO procedures, conducting and documenting hazard assessments, health testing and the list goes on. Many companies make the mistake of drafting their health and safety manual only to put it on the shelf to collect dust. Remember, this is your companies “safety bible” and spells out exactly what now needs to be managed on an ongoing basis in order to maintain OSHA compliance.
In addition to the requirements we’ve already discussed, the company must manage additional “administrative requirements” including their OSHA 300 logs (injury and illness records), record keeping and reporting requirements, as well as conducting routine inspections to identify and correct physical hazards which have a nasty way of popping up over and over again. The company must also manage an internal enforcement program to ensure that employees follow safety rules, such as wearing PPE.
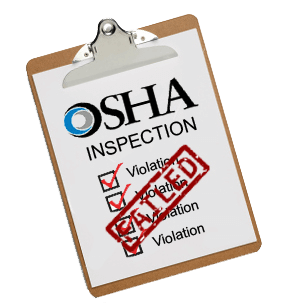
Risks & Liabilities For Failing To Manage OSHA Compliance:
It’s a lot to keep up with, but failure isn’t an option. These are Federal laws that impacted companies must follow or risk major risks and liabilities including serious employee injuries, surprise OSHA inspections that can result in fines and penalties that can run into the $tens or even $hundreds of thousands of dollars, criminal liabilities if a fatality occurs as a result of employer negligence ($250,000 fine and up to 6 months of jail time), and then there are civil liabilities that can result in $multi-million settlements if an employee get seriously injured as a result of employer negligence.
Companies who fail to manage workplace safety face additional liabilities & risks including lost money, lost business, higher insurance costs, damaged company reputation & PR nightmares, legal costs, increased employee turnover, embarrassment and more. It’s estimated that US companies lose $140 billion every year in combined direct and indirect costs associated with workplace injuries and illnesses.
Build a Strong Culture of Safety
We’ll begin to wrap up by pointing out that the key to the long term success of any safety program is building and managing a strong company safety culture.
As important as safety is for any company, managing it can be a challenging and often inconvenient process, meaning that the company must fully commit by building an underlying safety culture to help ensure it’s long term success. You can learn more about the 5 steps to building a strong company safety culture here.
What Now?
If you’re feeling a bit overwhelmed and confused at this point, don’t feel bad because you’re definitely not alone especially if you own or work for a small business. Small companies are at greatest risk because they almost always lack the time, money, resources and internal expertise needed to manage all of the complicated aspects of OSHA compliance.
Like any major project, it’s best to map out your plan, assign key roles and then take it one step at a time through to completion. As we stated earlier, the first step is to conduct a health and safety assessment of your workplace to determine which health and safety hazards exist and therefore which OSHA standards will apply to your company and safety program. This isn’t necessarily as easy as it sounds, and requires an experienced and qualified professional to get it done correctly.
Call 512-457-0374 or Click Here
To Schedule Your Free Consultation Today